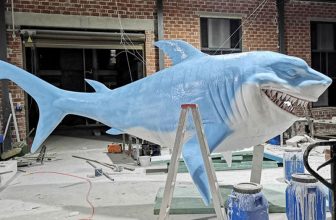
Case Studies
FDM (Fused Deposition Modeling) is a process fused deposition manufacturing (FDM) process developed by American scholar Scott Crump in 1988. FDM is the most widely used 3D printing technology and is usually the first 3D printing technology that people come into contact with. Fused Deposition Modeling (FDM) or Fused Filament Manufacturing (FFF) is an additive manufacturing process that belongs to the series of material extrusion. In FDM, an object is constructed by selectively depositing molten material in a predetermined path layer by layer. The material used is a thermoplastic polymer and is in the form of filaments.
Fused deposition modeling (FDM) or fused filament processing (FFF) belongs to the material extrusion series. In FDM, objects are constructed by selectively depositing molten materials layer by layer in a predetermined path. The materials used are thermoplastic polymers, most of which are filamentous wires. Recently, granular equipment has also appeared.
FDM is the most widely used 3D printing technology, accounting for the largest proportion of the global 3D printing installed capacity, and is usually the first 3D printing device that people come into contact with. The nature of the FDM process itself determines the relatively rough accuracy of the printed product, and it is more used in areas such as consumption, education, and cultural creation in the initial stage. However, in recent years, with the rapid development of 3D printing technology, some quasi-industrial-grade FDM equipment, and industrial and medical-grade FDM printing materials have emerged, which has greatly broadened the application fields of FDM technology.
The Internet of Things system of 3d-printing-china.com can realize one-click printing of hundreds of FDM devices, with a variety of materials and colors to choose from, whether it is a batch order or a large-size (acceptable splicing) sample. Delivery is completed in a short period of time.
PTJ meets or exceeds the quality standards of the world’s most demanding industries with our state of the art equipment and quality standards. Our precision and productivity is made possible by our ultimate success factor: the presence of skillful, knowledgeable PTJ experts in FDM 3d printing and more additive manufacturing parts.
The concept of 3D printing is no longer unfamiliar to us, because with the development of 3D printing technology, it has gradually integrated into our lives. 3D printed food, 3D printed toys, 3D printed cars, 3D printed biscuits, and even 3D printed houses, etc. Various 3D printed products. The fields involved in 3D printing include education, medical care, manufacturing, aerospace, military, etc., covering a very wide range. The reason why 3D printing is so powerful depends on a variety of technical routes, that is, a variety of printing methods.
FDM 3D printing technology is the most cost-effective way to produce custom thermoplastic parts and prototypes. Due to the high availability of the technology, the delivery cycle of FDM is very short (as fast as the next day delivery). And there are a variety of thermoplastic materials to choose from, suitable for prototyping and some non-commercial functional applications.
After the 3D printing model is completed, there will be some printing traces, and post-processing is required to achieve the desired effect. Using various post-processing methods, such as grinding and polishing, primer and painting, cold welding, steam smoothing, epoxy coating and metal plating, FDM 3D printed parts can be finished to very high standards.
Most FDM systems allow adjustment of several process parameters, including nozzle and build platform temperature, build speed, floor height and cooling fan speed. These are usually set by the operator, so the designer should rarely care about them.
From the designer’s point of view, what is important is the build size and layer height:
The usable internal dimensions of a desktop 3D printer are usually 200 x 200 x 200 mm, while for industrial machines, it can be as high as 1000 x 1000 x 1000 mm. If you want to use a desktop computer (in order to reduce costs), you can break the large model into smaller parts and then assemble it.
The typical layer height used in FDM varies between 50 and 400 microns and can be determined at the time of order. Smaller layer heights can produce smoother parts and more accurately capture curved geometries, while larger layer heights can be produced faster and at lower cost.
Industrial-grade FDM printers provide more powerful production capacity than desktop printers, with higher printing accuracy and larger print sizes.
Industrial-grade FDM printers can also print a wider range of materials, such as engineering plastics with high impact strength, biocompatibility, corrosion resistance, high temperature resistance, and flexibility. Although industrial-grade FDM printers are more expensive than desktop FDM printers, they are relatively simple to operate and low maintenance costs, which makes them a cost-effective solution for rapid prototyping and small-batch production operations.
At present, 3D printers are divided into two types: desktop-grade and industrial-grade. The difference between them is mainly in the forming size and printing accuracy. Generally speaking, the industrial-grade forming size is large and the printing accuracy is high, and the desktop-level forming size is small and the printing progress is low. Of course, with the update and iteration of 3D printers, the printing accuracy of desktop-level 3D printers has gradually improved.
If the printed part has a suspended part, the printer can print some substrates on the bottom first, and the suspended part of the part can be printed on the base. This part of the substrate plays a supporting role, which is the so-called “support”. After the model is printed, the support is usually removed by trimming. If it is a more elaborate model, the removal of support is sometimes a delicate task. Of course, the amount and position of the support are related to the placement of the model. The same model, different placement positions, will form different supports. Proper placement of the model can reduce support.
Support Material. As the name implies, it is the part that supports the molding material in the 3D printing process. After the printing is completed, the support material needs to be peeled off, so it also requires certain performance. The currently used support materials are generally water-soluble The material is soluble in water and easy to peel off. The specific characteristics requirements are as follows:
FDM technology requirements for supporting materials | ||
Performance | Specific requirements | Reason |
Temperature resistance | High temperature resistance | Because the support material must be in contact with the molding material on the support surface, the support material must be able to withstand the high temperature of the molding material without decomposition and melting at this temperature. |
Affinity with molding materials | Not wetted with molding material | The support material is an auxiliary method adopted in the processing, and must be removed after processing, so the affinity between the support material and the molding material should not be too good. |
Solubility | Water-soluble or acid-soluble | For prototypes with complex cavities and pores, in order to facilitate post-processing, the support material can be dissolved in a certain liquid to support it. Since the molding materials used in FDM are generally ABS engineering plastics, the materials can generally be dissolved in organic solvents, so organic solvents cannot be used. At present, water-soluble support materials have been developed. |
Melting temperature | Low | With a lower melting temperature, the material can be extruded at a lower temperature, which improves the service life of the nozzle. |
Liquidity | High | Since the molding accuracy of the support material is not high, in order to increase the scanning speed of the machine, the support material is required to have good fluidity, and relatively speaking, the viscosity can be worse. |
For hot melt extrusion (FDM) printers, the core component is the printer nozzle. Its function includes three aspects, namely (1) filament feeding; (2) heating; (3) extrusion.
Of course, the number of nozzles can also be multiple, and multiple nozzles can print a variety of different materials. For example, by printing materials of different colors, a better-looking model can be printed.
The commonly used materials for FDM printers are some thermoplastic materials, the main materials are PLA (environmental friendly materials), ABS, nylon, PHA, etc. In addition, mixing some wood fiber, metal powder, carbon fiber, etc. in PLA and ABS can print out models with woody, metallic, and high-strength performance; there are also luminous materials. After 15 minutes of exposure to this material, place it in Green light can be emitted in the dark.
PTJ offers online 3D printing services for china rapid prototyping and production of non-metal and metal 3D printed parts at affordable prices.
PTJ 3D Printing
Mobile WhatsApp WeChat:
+86 8288 6112
+86 152 1709 1354
Email: [email protected]
Address: Dongguan City, Guangdong Province, China.