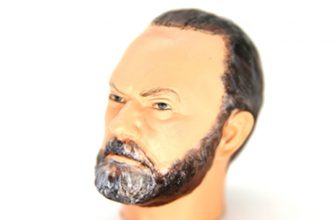
Case Studies
Stereolithography Technology (SLA) is a rapid prototyping technology that first appeared and realized commercialization in the world, and it is also one of the most in-depth and widely used rapid prototyping technologies. It mainly uses photosensitive resin as a raw material, and utilizes the characteristic that liquid photosensitive resin will cure quickly under ultraviolet laser beam irradiation. The photosensitive resin is generally liquid, and it immediately initiates a polymerization reaction and completes curing when irradiated with a certain wavelength of ultraviolet light (250 nm to 400 nm). SLA focuses on the surface of the light-curing material by focusing ultraviolet light of a specific wavelength and intensity to solidify it sequentially from point to line and from line to surface, thereby completing the drawing of a layered cross-section.
SLA is one of the three main technologies used in 3D printing, as well as Fused Deposition Modeling (FDM) and Selective Laser Sintering (SLS). It belongs to the category of photosensitive resin 3D printers. A similar technology usually combined with SLA is called digital light processing (DLP). It represents an evolution of the SLA process, using a projector screen instead of a laser.
Although not as popular as FDM technology, SLA is actually the oldest additive manufacturing technology. The term “stereolithography” is derived from ancient Greek. “Three-dimensional” and “(photo) lithography” mean “solid” and “light writing form” respectively.
As the oldest additive manufacturing technology, SLA is sometimes considered the “mother of all 3D printing technologies.” It was developed by the American company 3D Systems, which was founded by Chuck Hull in 1986. Hull coined the term “stereolithography” in 1986. He defined this technology as a method of making 3D objects by continuously printing thin layers of ultraviolet curing. Light.
In 1992, 3D Systems created the world’s first SLA device, which can manufacture complex parts layer by layer in a small amount of time. SLA was the first to enter the field of rapid prototyping in the 1980s and continues to develop into a widely used technology.
As in the case of many additive manufacturing processes, the first step involves designing a 3D model through CAD software. The generated CAD file is a digital representation of the desired object.
If they are not automatically generated, the CAD files must be converted to STL files. Standard Tessellation Language (STL) or “Standard Triangle Language” is the native file format of stereolithography software created by Abert Consulting Group in 1987 for 3D Systems. STL files describe the surface geometry of 3D objects, ignoring other Common CAD model attributes, such as color and texture.
The pre-printer step is to feed the STL file to 3D slicer software, such as Cura. These platforms are responsible for generating G-code, which is the native language of 3D printers.
SLA-level equipment has a pivotal role in the face of model proofing, industrial design, and the medical industry. The advantages of high-precision molding technology and rapid prototyping determine its ability to help advance in this type of industry.
When the process begins, the laser “pulls” the first layer of printed matter into the photosensitive resin. No matter where the laser hits, the liquid will solidify. A computer-controlled mirror guides the laser to the appropriate coordinates.
At this point, it is worth mentioning that most desktop SLA printers are upside down. In other words, the laser points to the build platform, which starts from a low position and gradually rises.
After the first layer, the platform is raised according to the layer thickness (usually about 0.1 mm) and the additional resin is allowed to flow under the already printed part. The laser then cures the next cross section and repeats the process until the entire part is complete. The resin that has not been contacted by the laser remains in the barrel and can be reused.
After the material is polymerized, the platform is raised from the tank and the excess resin is discharged. At the end of the process, the model is removed from the platform, the excess resin is washed, and then placed in a UV oven for final curing. Post-press curing allows the object to reach the highest possible strength and become more stable.
PTJ meets or exceeds the quality standards of the world’s most demanding industries with our state of the art equipment and quality standards. Our precision and productivity is made possible by our ultimate success factor: the presence of skillful, knowledgeable PTJ experts in sla 3d printing and more additive manufacturing parts.
The printing material of SLA is a liquid resin. During the curing process, the monomer carbon chains that make up the liquid resin will be activated by the UV laser and become solid, thereby forming a strong and indestructible bond between each other. The photopolymerization process is irreversible, so SLA parts cannot be converted back to a liquid state, and they will burn rather than melt when heated.
The height of the printing layer in the SLA process is between 25 and 100 microns. Lower layer heights can more accurately capture curved geometries, but will increase build time (and cost) and the possibility of printing failures. A layer height of 100 microns is suitable for most common applications.
The construction area is another parameter that is very important to the designer. The build size depends on the type of SLA machine. 3d-printing-china.com 3D’s supply chain system has almost all types of SLA equipment on the market, with full coverage of construction area (printing size) and printing materials.
SLA’s 3d printing process principle determines that a supporting structure must be required during the printing process. The support structure is printed with the same material as the part and needs to be removed manually after printing. The direction in which the part is printed determines the position and number of supports. The print placement is to properly orient the parts so that the visual critical surface does not contact the supporting structure.
The bottom-up and top-down SLA printer usage support methods are different:
For thicker models, if shelling does not affect its performance, it is recommended to shell out, which can reduce the weight of the model and reduce the cost of the model. For large-surface models, it is recommended to add stiffeners after shelling, which can greatly reduce the degree of deformation of the model. Of course, this should be based on the specific analysis of the structure of the model. The minimum wall thickness requirement of the SLA process is related to the overall size. As the product size increases, the wall thickness should be increased accordingly. For small size parts (≤200mm) and medium size parts (200-400mm), the recommended minimum wall thickness is 2mm. For large size parts (≥400), the minimum wall thickness is recommended to be greater than 3mm.
As mentioned earlier, the SLA process needs to add support to the cantilever. The critical value of the cantilever angle is generally 35°. Therefore, the angle between the cantilever and the bottom surface can be designed to be greater than 35 when the model is designed without affecting the performance of the model. °, adding rounded corners when appropriate can reduce the support and ensure the model size and surface quality.
For concave text or surface details, it is generally recommended that the line width is at least 0.35mm and the depth is 0.35 mm. For raised text or surface details, it is recommended that the width be at least 0.35mm and the protrusion height should be at least 0.35 mm.
The assembly model generally has multiple independent shells. For the assembly that is easy to disassemble, we choose to disassemble and print, so that it will not affect the free placement of various parts and the best surface quality of the product. It is generally recommended to assemble The gap> 0.3mm.
But for some movable models that are printed in one piece, some parts cannot be disassembled, of course, they can also be printed. Generally, it is recommended that the assembly gap is ≥0.4mm, otherwise it may be printed as one with other parts.
Sometimes for printing convenience, you can also use support beams to connect all the shells, so that you can ensure that your parts will not be lost during mass printing. Generally, it is recommended that the thickness of the support beam is not less than 3mm.
The placement of the model has a great influence on the surface quality and strength of the product. Generally, it is recommended that the complex features of the workpiece face up, and the step texture of the curved workpiece horizontally is very obvious. Similar to a contour map, it is generally recommended to be 45° with the bottom surface of the platform. Place it at an angle of ° or upright, the long workpiece and the scraper are generally placed vertically or at an angle of 45°.
For oversized pieces that exceed the size of the printing platform, splicing can be used, and the splicing gap is generally recommended to be greater than 0.3mm. When splicing, you can add triangles, rectangles, serrations, bosses and pin types for positioning and connection, and use AB glue for bonding.
In order to ensure the smooth flow of the liquid resin from the cavity of the model after the shell is extracted, to reduce the weight of the model and reduce the cost of model production, holes should be made on the non-important surface of the model. The aperture diameter is related to the size of the model’s open surface, but it is generally recommended The minimum aperture is 3mm and the maximum is 30mm. The specific design should be based on the size of the model and the specific structure. After the post-processing is completed, the process holes can be blocked, and the notches can be used for positioning, and then a proper amount of polishing is enough.
For simple coloring parts, you can use integrated printing and then coloring. For complex coloring parts, the coloring model should be disassembled according to the coloring requirements, and then assembled after coloring. The assembly principle is in accordance with the splicing principle. Leave connection structure and gaps.
Each technology has its own advantages and limitations, but which technology is most suitable for you What about the job requirements? In 3D printing, whether it is metal printing, plastic printing, powder printing, all 3D printing technologies are based on a common principle, cutting the 3D model horizontally into separate cross-sections. We call this step slicing. Then print on the platform one by one upwards, and finally form a three-dimensional object. However, the three technologies of SLA and LCD use different molding techniques to print these cross-sectional layers.
Desktop-level SLA printing technology is the same. It uses resin consumables. Unlike LCD, the curing light wavelength of his resin consumables. When facing different wavelengths of light, the corresponding wavelength resin consumables should be used to avoid affecting the printing quality. The SLA desktop-level molding method is very similar to LCD. It consists of three major parts: resin feeder, printing platform, and laser transmitter. When printing, pour resin consumables into the resin feeder, the platform is lowered into the feeder, and the laser transmitter According to the shape of the slice layer, the resin in the trough will be scanned and cured through a laser galvanometer, and it will rise layer by layer to obtain a fine three-dimensional model. Because the SLA molding process is a laser scanning curing process, the molding accuracy is very high and the speed is fast, and the laser scanning speed can reach 5M/S.
PTJ offers online 3D printing services for china rapid prototyping and production of non-metal and metal 3D printed parts at affordable prices.
PTJ 3D Printing
Mobile WhatsApp WeChat:
+86 8288 6112
+86 152 1709 1354
Email: [email protected]
Address: Dongguan City, Guangdong Province, China.