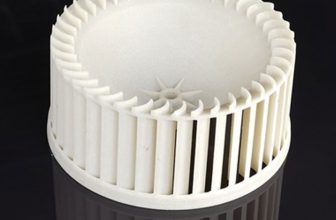
Case Studies
Selective laser sintering (SLS) is a powerful 3D printing technology that belongs to the powder bed fusion process series, which can produce high-precision and durable parts, which can be directly used for end-use, small batch production or prototype prototypes. In the printing process of the SLS equipment, a high-power laser is used to fuse small particles of plastic powder into the required three-dimensional shape. The laser selectively fuse powder materials by scanning the three-dimensional data section on the surface of the powder bed. After scanning each section, the powder bed is reduced by a layer of thickness, a new layer of material is added to it, and the selective laser sintering process is repeated until the part is completed.
SLS 3D printing can be used not only for the prototype design of functional polymer components, but also for small production runs because it has high design freedom, high precision, and produces parts with good and consistent mechanical properties.
SLS uses the principle of sintering powder materials under laser irradiation, and the computer controls the layer-by-layer formation. The SLS technology also uses layered stacking molding. The difference is that it first lays a layer of powder material, preheats the material to close to the melting point, and then uses a laser to scan the cross section of the layer to raise the temperature of the powder to the melting point. Sintering to form a bond, and then repeat the process of powder spreading and sintering until the entire model is formed.
SLS (selective laser sintering process), this process was proposed by C.R.Dechard of the University of Texas in 1989, and then C.R.Dechard founded DTM company and released the industrial-grade commercial 3D printer Sinterstation based on SLS technology in 1992.
As in the case of many additive manufacturing processes, the first step involves designing a 3D model through CAD software. The generated CAD file is a digital representation of the desired object.
If they are not automatically generated, the CAD files must be converted to STL files. Standard Tessellation Language (STL) or “Standard Triangle Language” is the native file format of stereolithography software created by Abert Consulting Group in 1987 for 3D Systems. STL files describe the surface geometry of 3D objects, ignoring other Common CAD model attributes, such as color and texture.
The pre-printer step is to feed the STL file to 3D slicer software, such as Cura. These platforms are responsible for generating G-code, which is the native language of 3D printers.
When the process begins, the laser “pulls” the first layer of printed matter into the photosensitive resin. No matter where the laser hits, the liquid will solidify. A computer-controlled mirror guides the laser to the appropriate coordinates.
At this point, it is worth mentioning that most desktop SLS printers are upside down. In other words, the laser points to the build platform, which starts from a low position and gradually rises.
After the first layer, the platform is raised according to the layer thickness (usually about 0.1 mm) and the additional resin is allowed to flow under the already printed part. The laser then cures the next cross section and repeats the process until the entire part is complete. The resin that has not been contacted by the laser remains in the barrel and can be reused.
After the material is polymerized, the platform is raised from the tank and the excess resin is discharged. At the end of the process, the model is removed from the platform, the excess resin is washed, and then placed in a UV oven for final curing. Post-press curing allows the object to reach the highest possible strength and become more stable.
PTJ meets or exceeds the quality standards of the world’s most demanding industries with our state of the art equipment and quality standards. Our precision and productivity is made possible by our ultimate success factor: the presence of skillful, knowledgeable PTJ experts in sls 3d printing and more additive manufacturing parts.
SLS printing technology uses powder spreading to spread a layer of powder material on the upper surface of the formed part and heat it to a temperature just below the sintering point of the powder. The control system controls the laser beam to be on the powder layer according to the cross-sectional profile of the layer. Scan upwards to raise the temperature of the powder to the melting point for sintering and bonding with the molded part below After one layer is completed, the workbench drops a layer of thickness, and the spreading roller spreads a layer of uniform and dense powder on it, and sinters the section of the new layer until the entire model is completed.
When the workpiece is completely formed and completely cooled, the workbench will rise to its original height. At this time, the workpiece needs to be taken out and the powder on the surface of the model needs to be removed using a brush or compressed air.
The SLS process supports a variety of materials, no support structure is required for the formed workpiece, and the material utilization rate is high. Although the price of SLS equipment and the price of materials are still very expensive, the materials need to be preheated before sintering, and the materials will volatilize during the sintering process, and the equipment working environment is relatively demanding.
Since SLS does not require supporting materials, parts with hollow parts can be printed easily and accurately.
Because the hollow part uses less material, it can reduce the weight and cost of parts, which is particularly important in aerospace. Therefore, in the design process of the part or the data processing process before printing, it is necessary to consider the powder escape hole to remove the unsintered powder from the inside of the component (supporting during the sintering process). It is recommended to add at least 2 escape holes with a minimum diameter of 5 mm in your design.
If stronger stiffness is required, the part must be completely solid printed. Another option is to make a hollow design, eliminating the need for escape holes. In this way, the tightly packed powder will be trapped in the part, thereby increasing its mass and providing some additional support to resist mechanical loads without affecting manufacturing time. The internal honeycomb grid structure can be added to the hollow interior to further improve the rigidity of the component
The main advantage of SLS is that it does not require a supporting structure. The unsintered powder provides all the necessary support for the part. Therefore, SLS can be used to create free geometric shapes. As long as it is within the parameters of the printing process, designers can display their talents as they want without worrying about manufacturing issues.
When using SLS for printing, especially for small batch production, it is very important to make full use of the entire build volume and increase the printing volume ratio (the volume ratio of the printed product in the entire printing chamber). According to the layout requirements of the printed products, after the maximum printing height is determined, it will take approximately the same time to print regardless of the number of printed products in the print control. This is because the powder spreading speed of each layer determines the total printing time (laser scanning occurs very quickly), and the machine will have to cycle through the same number of layers.
Therefore, for a factory doing SLS process 3D printing services, a large number of orders can be used, and the order products can be optimally combined as much as possible for production in the same printing warehouse, which will greatly reduce printing costs and increase printing speed. (Reduce the time to wait for orders and collect orders, and quickly start production). 3d-printing-china.com and AI order dispatch and order consolidation system solve this problem well and provide customers with comprehensive solutions with the best cost performance.
PTJ offers online 3D printing services for china rapid prototyping and production of non-metal and metal 3D printed parts at affordable prices.
PTJ 3D Printing
Mobile WhatsApp WeChat:
+86 8288 6112
+86 152 1709 1354
Email: [email protected]
Address: Dongguan City, Guangdong Province, China.