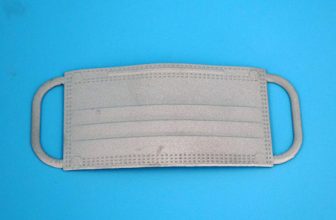
Case Studies
DLP is the abbreviation of "Digital Light Procession", which is the digital light processing 3D printing molding technology, which is called the digital light processing rapid prototyping technology, which means that this technology must first digitally process the image signal, and then project the light come out. It is based on the digital micromirror component-DMD (Digital Micromirror Device) to complete the visual digital information display technology. To be more specific, DLP projection technology uses digital micromirror wafer (DMD) as the main key processing element to realize the digital optical processing process. The basic principle is to use a digital light source to project layer by layer on the surface of the liquid photosensitive resin in the form of surface light, and then solidify and shape layer by layer. DLP technology has many similarities with SLA, and its working principle is also the use of liquid photosensitive polymer to cure under light. DLP technology uses a higher-resolution digital light processor (DLP) to solidify liquid polymer, solidifying the liquid polymer layer by layer, and so on until the final model is completed. DLP molding technology generally uses photosensitive resin as the printing material.
DLP is a 3D printing molding method. In the competition of many brands, PTJ is loved by the public because of its diversified materials and high molding accuracy. Serviced industrial design, toy animation, jewelry, dental prosthesis, ear hearing and medical treatment etc.,
PTJ meets or exceeds the quality standards of the world’s most demanding industries with our state of the art equipment and quality standards. Our precision and productivity is made possible by our ultimate success factor: the presence of skillful, knowledgeable PTJ experts in DLP 3d printing and more additive manufacturing parts.
Compared with other 3D printing process equipment, because the projection pixel block of DLP 3D printing equipment can achieve a size of about 50μm, it can print products with higher detail accuracy requirements, so as to ensure that the processing size accuracy can reach 20~30μm, and the surface projection The characteristics also make it more efficient in processing. The projection structure of the equipment is mostly integrated, which makes the layer curing and forming function modules smaller, so the overall size of the equipment is smaller. The characteristics of its molding are mainly reflected in the following points:
DLP light-curing 3D printers have unique advantages over other 3D printers. First of all, there is no moving beam, and the printing vibration deviation is small; there is no movable nozzle, there is no material blocking problem at all; there is no heating part, which improves electrical safety; and the printing preparation time is short. save energy.
Secondly, the amount of consumables added is far less than other equipment, saving users’ costs. In addition, DLP can manufacture finer parts, such as jewelry and dental molds.
Compared with other large 3D printers, DLP printing technology cannot print large objects, so most of them are desktop 3D printers, which are mainly used in medical, jewelry, education and other fields.
For a heavy model, if it does not affect its performance, it is recommended to hollow out, which can reduce the weight of the model and reduce the cost of the model. This can greatly reduce the material cost of the model. Of course, this should be based on the specific analysis of the model structure, DLP The minimum hollowed-out wall thickness requirement of the process is related to the overall size. As the product size increases, the wall thickness should be increased accordingly. It is generally recommended that the minimum wall thickness is 1.2mm. For compression-molded mass-produced parts, a minimum wall thickness of 1.5mm is recommended.
The DLP process needs to add support for the suspended part. The critical value of the cantilever angle is generally 35°. Therefore, without affecting the performance of the model, the angle between the suspension and the bottom surface can be designed to be greater than 35° during the model design, and the angle can be added when appropriate , Can reduce the support, ensure the model size and surface quality.
For concave text or surface details, it is generally recommended that the line width is 0.15mm and the depth is 0.15 mm. For raised text or surface details, it is recommended that the width be at least 0.15mm and the height of the protrusion should be at least 0.15 mm.
The assembly model generally has multiple independent shells. For the assembly that is easy to disassemble, we choose to disassemble and print, so that it will not affect the free placement of various parts and the best surface quality of the product. It is generally recommended to assemble The gap is> 0.1mm.
However, for some movable models that are printed in one piece, some parts cannot be disassembled, and of course they can be printed. Generally, it is recommended that the assembly gap is ≥0.25mm, otherwise it may be printed as one with other parts.
Sometimes for printing convenience, you can also use support beams to connect all the shells, so that you can ensure that your parts will not be lost during mass printing. Generally, it is recommended that the thickness of the support beam is not less than 2mm.
PTJ offers online 3D printing services for china rapid prototyping and production of non-metal and metal 3D printed parts at affordable prices.
PTJ 3D Printing
Mobile WhatsApp WeChat:
+86 8288 6112
+86 152 1709 1354
Email: [email protected]
Address: Dongguan City, Guangdong Province, China.